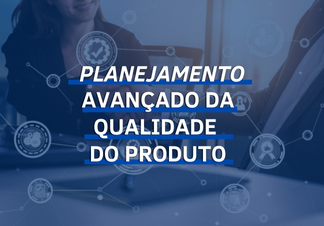
Use of APQP at developments by Samot
With the need for more robust processes that ensure the quality of products developed, it is necessary to use project management tools that encompass all company areas, from Commercial to Customer Service, from planning to delivery of the finished product.
The tool used at Samot to meet this need for standardization is APQP (Advanced Product Quality Planning). This manual was developed in the 1980s by specialists from major car manufacturers: Ford, General Motors and Chrysler.
*Image 1: Advanced product quality and control planning
This manual presents the best practices in the development of products and processes, divided into five different phases:
Phase 1 – Planning: In this phase, there is commercial contact with the client, where all needs and expectations are aligned internally, resulting in the possibility of moving on or not with the development.
Phase 2 – Product design and development: In this step, the planning process elements are discussed, where design aspects and characteristics are developed almost in the definitive format. A preliminary feasibility analysis must be conducted to assess potential issues that may occur during manufacturing.
Phase 3 – Process design and development: In this step, the main aspects of the manufacturing system development and its respective control plans are discussed. It is expected that the manufacturing system ensures that requirements, needs and expectations from the client are met.
Phase 4 – Product and Process Validation: In this step, the main characteristics of validations for the manufacturing process are discussed through assessment of a pilot production run. In this pilot run, it is assessed whether the control plan and the flow are being followed correctly and if the product requirements are fully met.
Phase 5 – Feedback, Assessment and Corrective Action: In this step, the item manufacturing is validated, when all common and special causes for variation are present. It is necessary to check whether all actions expected were concluded and feed the database back with lessons learned.
All these phases are followed to ensure reliable products at the end of development, with the right resources and the necessary quality, in addition to having used costs according to prior analysis conducted by the Commercial area.
This APQP system also adds other manuals that are equally important for development, such as: CEP, FMEA, MSA and PPAP. Using these manuals is the foundation for Samot to ensure the reliability, quality and robustness of our processes.